The rubber is in a high elastic state at normal temperature. When the temperature falls below its crystallization temperature, the rubber enters a crystalline state. When the temperature rises to a certain critical point (which varies with the rubber type), it changes from a high elastic state to a viscous flow state, and becomes a high-viscosity viscous body that can flow. At this time, under the action of an external force, the rubber exhibits a fluid state, thereby obtaining fluidity.
It is the fluidity that gives the rubber a series of processing characteristics required for processing, and meets the needs of processing such as calendering, extrusion, filling, and injection molding.
The basis of rubber fluidity is the characteristics of non-Newtonian fluids. Non-Newtonian fluids differ from Newtonian fluids in low molecular materials. They are subject to “Newtonian Flow Law J. Fluids are low viscosity and viscosity changes with temperature. Non-Newtonian fluids are not subject to Newton’s law of flow. “There is internal friction between the layers, which creates resistance to material flow. There are two ways to mitigate this resistance.”
First, applying a shear force to the material;
Second, raise the processing temperature. This is an effective method often used in rubber processing.
Figure 4-5 is a flow curve for Newtonian and non-Newtonian liquids. The difference in the direction of the curve can fully explain this problem.
Liquidity curve.
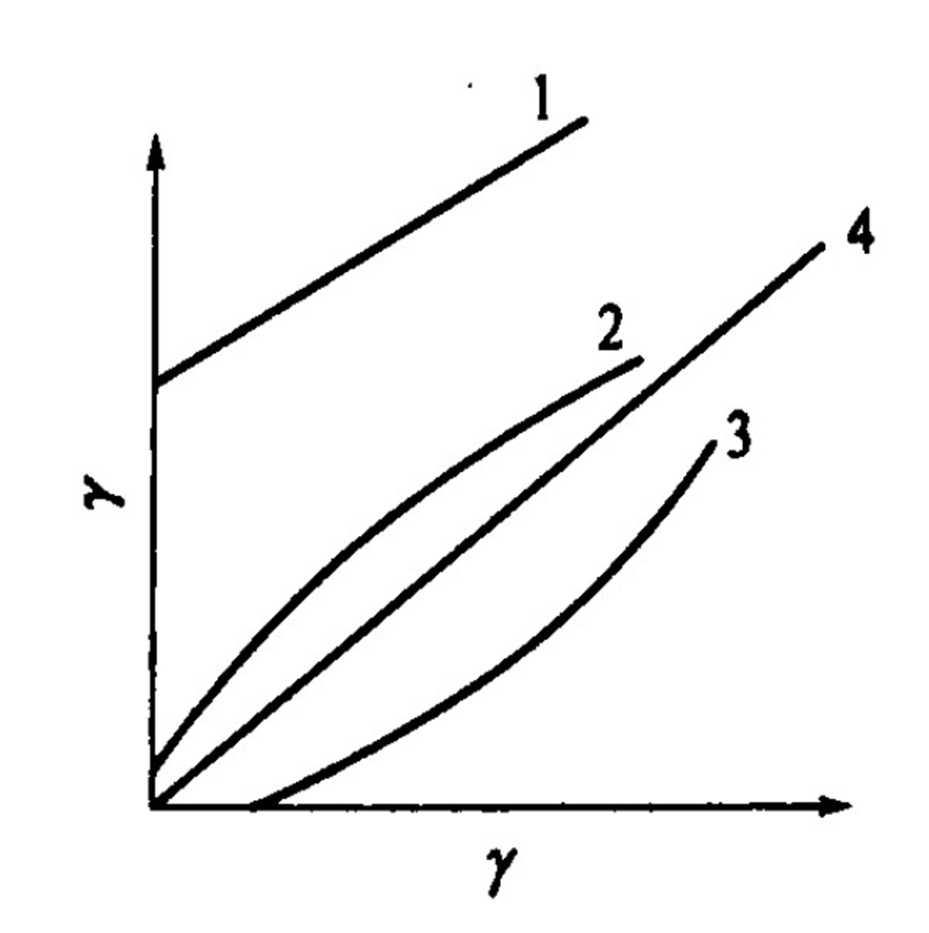
Two of them are typical flow curves for rubber and four are Newtonian fluid flow curves. The biggest feature of 4 is that the shear stress (ordinate) is proportional to the viscosity (abscissa). As far as rubber is concerned, the role of fluidity is very important. Through the flow, the processing of each process can be realized, and quality problems such as lack of glue, flow marks and delamination can be avoided.